Rope Access Kit, what is in it?
Equipment used for working at height, rope access, and rescue systems is specially developed, engineered, and tested to fulfill the needs of a modern work-at-height system. The essential requirement is that equipment can be utilized for multiple applications. This reduces the amount of gear a technician requires and ensures that the technician has everything on […]
Rope colours and why we choose them
Rope colours and why we choose them, there are many reasons here are some of them: Price—yes, price is king, and white is the cheapest rope among a range of colours. White is the natural colour of the yarns used to make ropes. The yarns are then treated with a dye to give them colour. […]
Product standards
For a manufacturer product standards are important. Rope rescue, rope access, tree work, tower climbing, etc., are all work-related activities that must meet certain standards. Certification depends on where you are. In Canada, all these different industries have their own set of rules. They can vary for each province, making it hard to follow what […]
Eyolf origin story
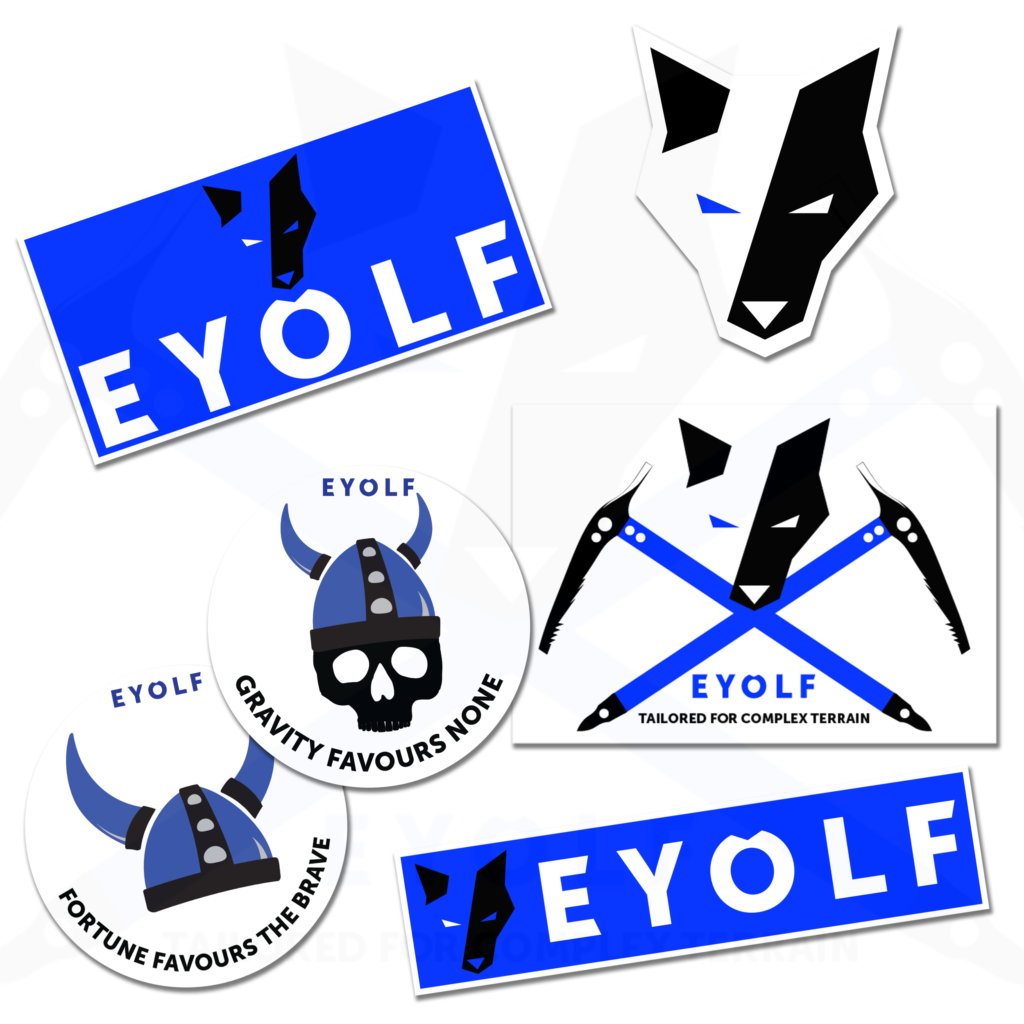
Eyolf origin story isn’t one of constant success. Nothing happened overnight or with a group of friends who thought it would be cool to make some gear. Nope. Instead, it started with the need to survive, opportunity, hard work, and dedication. From day one, it was clear that we would stand for providing great […]
Better. Could you say better?
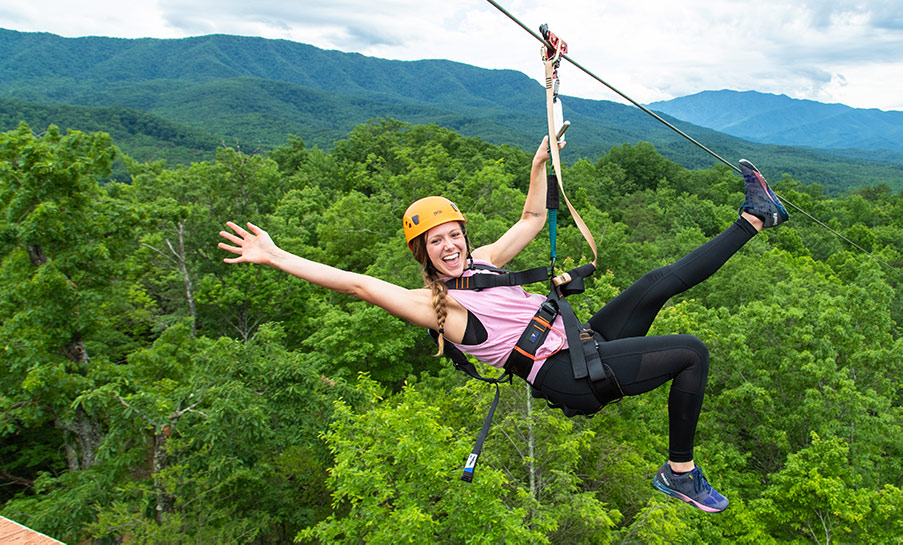
Could you say better? It is a bold statement to make. Our customers keep telling us that our products are better, so it must be true, right? We want to explain why we think our harnesses are better. Let’s start with the structure of the harness. Most of our webbing is industrial grade, and because […]
Regarding Disinfecting Equipment
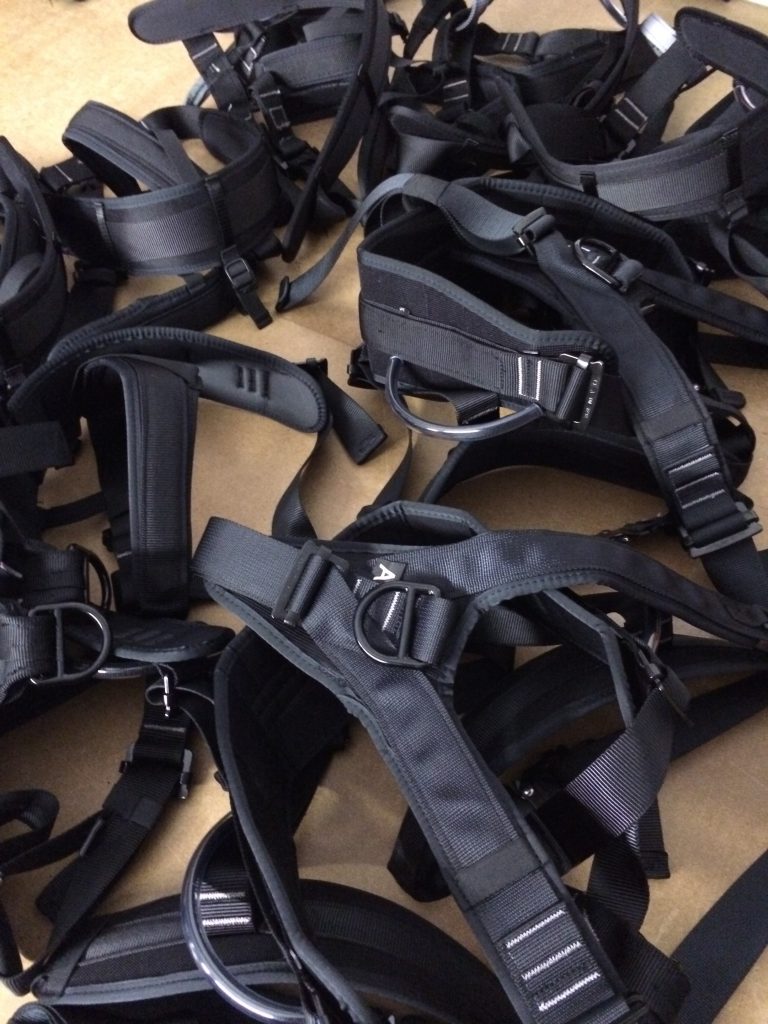
Here is a guideline for disinfecting your equipment in the most feasible way. Many of us are affected by the COVID-19 pandemic and hope to resume business as usual. Therefore, we currently abide by regulations set forth by the Canadian government regarding the operation of our business at this time. Furthermore, our operation guidelines are […]
Rope Access Work Advice
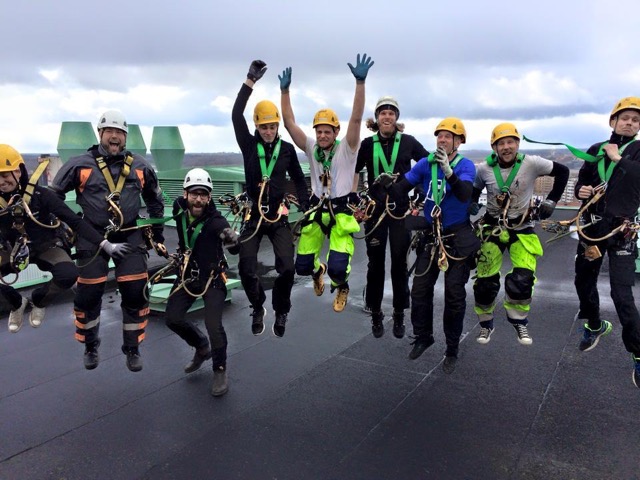
In the “rope access industry,” we often get the same questions from newcomers, such as “How can I get into this exciting industry?” or “Where do I get training, and what kind of training do I need?”. A long time ago, I asked a good friend of mine to help someone new to our industry, […]
Working with legislation on the job
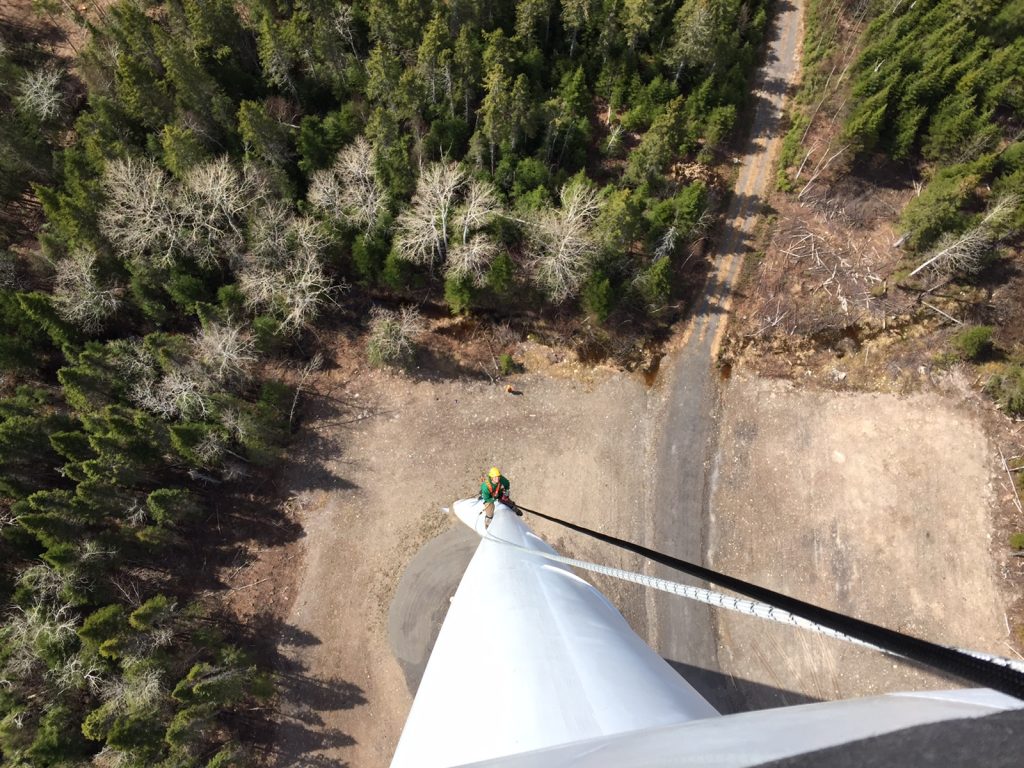
One of our many services is educating business owners, supervisors, and technicians on how to comply with legislation regarding working at height. This is a complicated matter that most Health and Safety Officials don’t comprehend well enough to give well-informed advice. The Health and Safety Official assigned to a project has much to consider. They […]
Fall Protection
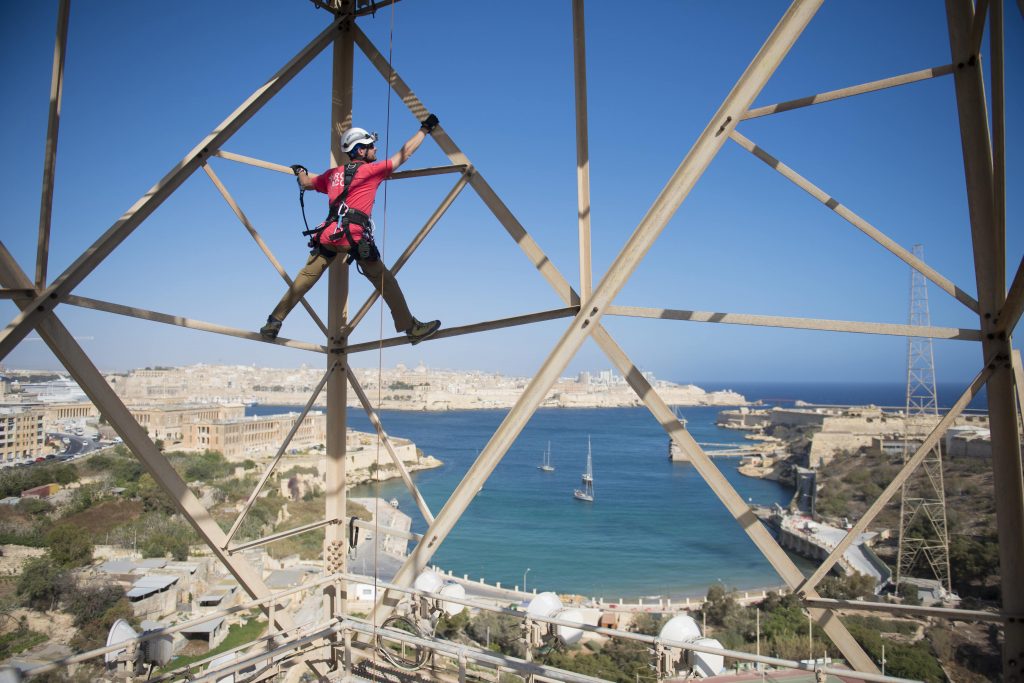
When considering fall protection, fall arrest is expected to be regarded as the only option. When protection against falling is needed, most go to a safety store and buy fall arrest equipment. Which may or may not address their needs. Certain companies have worked this angle for a long time to exacerbate the situation, offering […]
Our new home
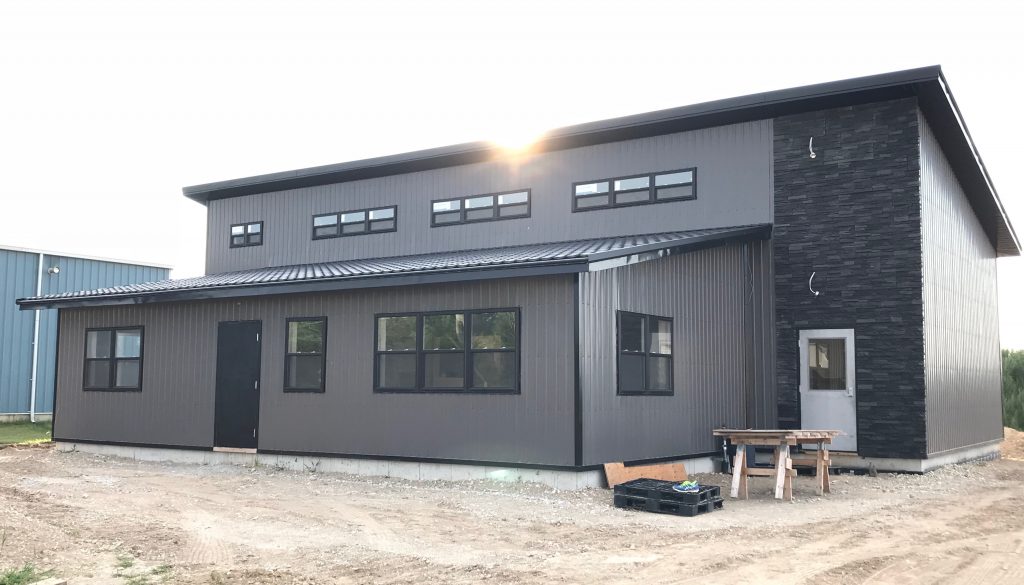
We believe change is a good thing here at Eyolf, which is why you can expect to see our brand-new production centre opening later this year. Curious about our progress? Follow along on Facebook and Instagram.